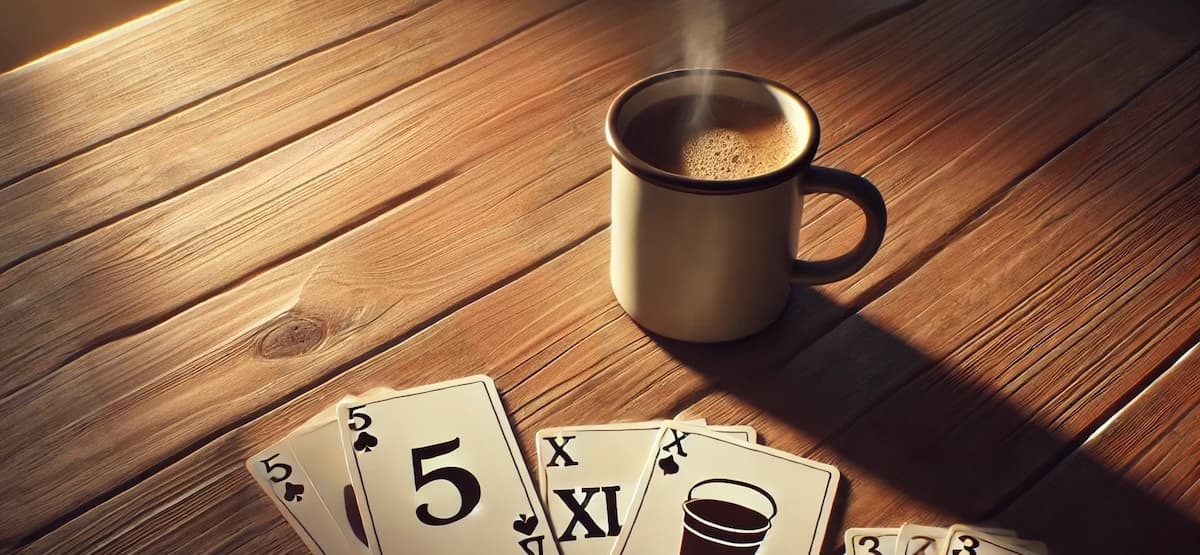
Did you know that prioritizing efficiency in business operations can lead to a 60% profitability boost? This is why striving for efficiency and value delivery is more crucial than ever. This quest has led to the widespread adoption of lean thinking, a philosophy aimed at maximizing value by eliminating waste.
Toyota's implementation of lean principles revolutionized its operations, setting a benchmark for industries worldwide. This blog will explore the core principles of Toyota's lean thinking and how agile teams can benefit from similar methodologies
Lean thinking involves creating more value for customers with fewer resources by optimizing processes and eliminating waste. Toyota's adoption of lean principles, known as the Toyota Production System (TPS), transformed its manufacturing operations, leading to unparalleled efficiency and quality. The success of TPS inspired numerous industries, from healthcare to software development, to implement lean principles and significantly improve their operations.
Philosophy:
Long-Term Vision: At the heart of Toyota's lean thinking is a long-term philosophy prioritizing respect for people and sustainable growth over short-term gains. This approach ensures that decisions made today will benefit the organization and its stakeholders in the future.
Cultural Impact: A long-term philosophy fosters a strong, values-driven culture where respect, teamwork, and continuous improvement are paramount.
Process:
Right Processes: Toyota emphasizes following the right processes to achieve desired outcomes. This involves standardized procedures that ensure efficiency and quality.
Gemba: Leaders are encouraged to go to the Gemba—the actual place where work is done—to understand problems firsthand and develop practical solutions. This hands-on approach ensures that leaders are aware and connected to the realities of the work environment.
People:
Employee Development: Toyota invests heavily in training and empowering its employees. This commitment to development fosters a culture of continuous improvement where every team member contributes to the organization's success.
Culture of Continuous Improvement: Toyota creates an environment of constant innovation and improvement by empowering employees.
Problem-Solving:
Structured Methods: Toyota employs structured problem-solving methods to address issues, ensuring effective and sustainable solutions.
Root Cause Analysis: Techniques such as the 5 Whys are used to identify and solve the root causes of problems, preventing recurrence and promoting long-term stability.
Agile teams can maximize their success by adopting the four pillars of Toyota's lean thinking:
Philosophy:
Long-Term Success: Agile teams should prioritize sustainable growth and respect for individuals over short-term wins. This approach leads to more robust and resilient teams.
Value-Driven Culture: Building a culture that values long-term achievements and team well-being ensures that all team members are aligned with the organization's goals.
Process:
Effective Processes: Agile practices like iterative development and continuous feedback ensure that teams follow the right processes to achieve desired outcomes.
Direct Engagement: Leaders should spend time with their teams to understand challenges and opportunities, mirroring Toyota's Gemba approach.
People:
Continuous Development: Investing in training and skills development for agile team members fosters a culture of growth and continuous improvement.
Empowerment: Encouraging team members to take ownership of their work and contribute to improvements enhances motivation and innovation.
Problem-Solving:
Structured Approach: Using agile methodologies like retrospectives to address and resolve issues ensures that problems are tackled effectively.
Focus on Root Causes: Applying techniques like the 5 Whys helps teams identify and solve the root causes of problems, leading to sustainable solutions.
Just-In-Time (JIT) Production: JIT focuses on producing only what is needed when it is required and in the amount needed. Benefits:
Reduced Waste: Minimizing excess inventory and associated costs.
Improved Efficiency: Streamlining production to match demand.
Enhanced Flexibility: Quick response to changes in customer demand.
Jidoka (Autonomation): Jidoka involves adding automation with a human touch to detect and stop defects. Benefits:
Higher Quality: Immediate detection and correction of defects.
Reduced Defects: Preventing defective products from accumulating.
Empowered Teams: Encouraging workers to stop the line to address issues.
Kaizen (Continuous Improvement): Emphasizing continuous, incremental improvements. Benefits:
Ongoing Improvement: Small changes lead to significant long-term gains.
Employee Engagement: Fostering a culture of collaboration and innovation.
Cost Savings: Reducing waste and lowering operational costs.
Heijunka (Leveling Production): Leveling production to avoid batching and bottlenecks. Benefits:
Stable Workload: Maintaining a consistent workload to reduce stress.
Improved Flow: Ensuring smoother workflow and reducing bottlenecks.
Better Resource Utilization: Optimizing resource allocation and minimizing idle time.
5S (Workplace Organization): Organizing and standardizing the workplace for efficiency and safety. Benefits:
Increased Efficiency: Reducing time spent searching for tools and materials.
Enhanced Safety: Clean and organized workspaces reduce accident risks.
Consistency: Standardizing processes ensures consistent output.
Poka-Yoke (Error Proofing): Designing processes to prevent errors or make them immediately detectable. Benefits:
Reduced Errors: Minimizing the occurrence of mistakes.
Higher Quality: Ensuring higher quality products by preventing defects.
Cost Savings: Decreasing rework and associated costs.
Hoshin Kanri (Policy Deployment): Aligning organizational goals with projects through clear objectives and metrics. Benefits:
Alignment: Ensuring team efforts are aligned with strategic goals.
Focus: Prioritizing key initiatives and allocating resources effectively.
Accountability: Providing a framework for tracking progress and accountability.
Toyota's lean thinking principles offer invaluable insights and methods for agile teams striving for efficiency and excellence. By embracing these lean alternatives, teams can enhance their processes, reduce waste, and deliver higher customer value. Continuous improvement and focusing on long-term success are vital to thriving in today's competitive landscape.
At Team O'Clock, we are dedicated to helping agile teams achieve their full potential through effective lean methodologies. Our expertise and tools support your journey towards creating more value with fewer resources, driving sustainable growth, and maintaining a competitive edge.
Choose Team O'Clock to guide you in implementing these proven strategies by signing up for a 15-day free trial.
Assist your team's growth with our partnership program: